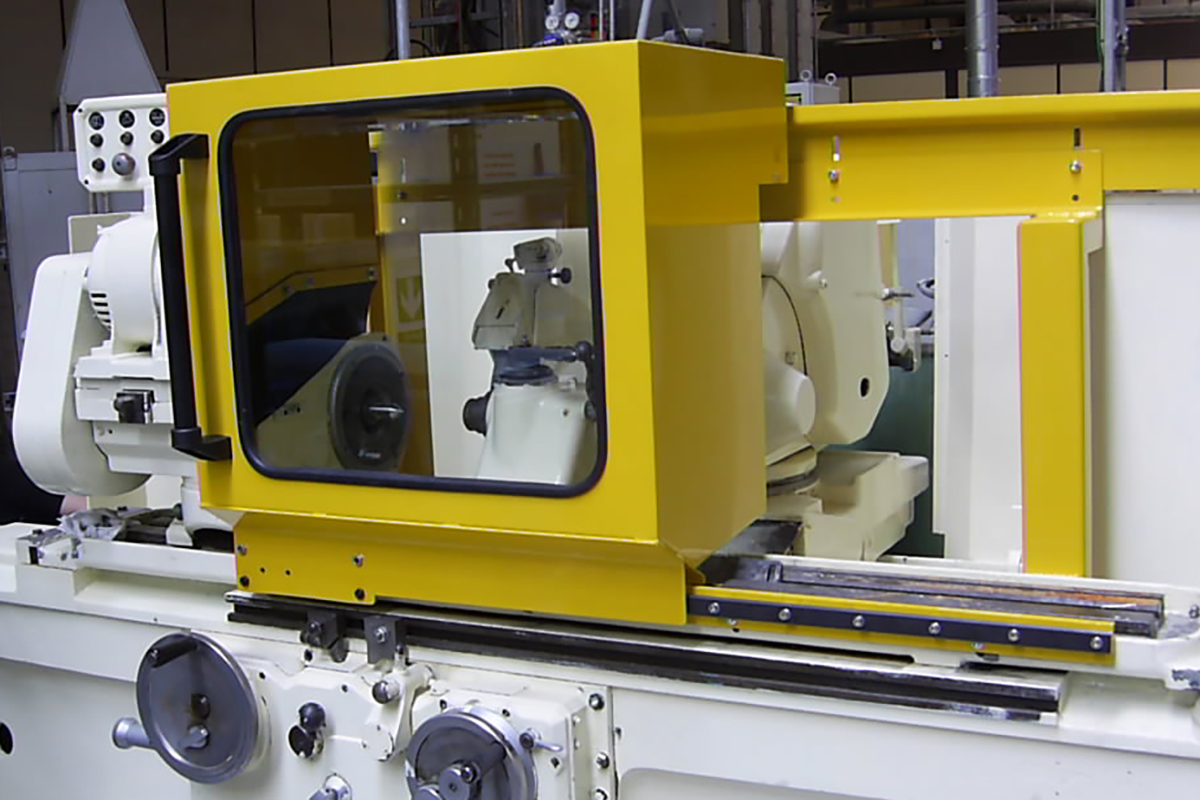
Safety Matters – Manufacturing
Creating a Safer Workplace with Point-of-Operation Guards
The machines used in today’s manufacturing operations are designed to maximize worker safety. Yet, even the newest, most modern equipment can be vulnerable from a safety perspective. For example, some of the most dangerous hazards on the work floor exist around a machine’s point of operation, such as the blade of a saw or the slide of a power press.
To ensure the safety of your workers, it’s important that points of operation be properly outfitted with guards to prevent injuries and accidents. However, effective guarding for hazardous motions is not always simple. Improper guarding could not only result in inadequate protection for your workers, but also cause a defect in the machine itself. The correct guard for the point of operation will depend on the machine in use.
Common types of guards that workers should be familiar with include:
- Fixed guards: These types of guards are permanently affixed to their equipment. Due to its simplicity, a fixed guard is usually preferable to other types, but can cause issues with visibility, flexibility of suitable operations and with the need to be removed for repair or adjustments to equipment.
- Interlocked guards: These guards provide easier access than fixed guards, but include a failsafe that will automatically power down the machine if opened or removed. The machine cannot be restarted until the guard has been replaced. Replacing the guard will not automatically restart the machine. This type of guard can provide maximum protection while also allowing easy access to the machine, but may cause unintended shutdowns and require careful adjustment and maintenance.
- Adjustable guards: Adjustable guards are advantageous in that they allow a wide variety of sizes and materials to be used in the machine. Employees working with adjustable guards should be aware that protection may not be complete at all times and that their hands may come closer to point of operation hazards than with other guards. These guards can also interfere with visibility and require frequent adjustment.
- Self-adjusting guards: As the name suggests, these guards adjust themselves according to the stock being fed into the machine. As the operator pushes material into the danger area, an opening only large enough for the stock is created. These guards provide a constant barrier between the danger area and the operator but may not provide maximum protection, can disrupt visibility and might need frequent maintenance and adjustment.
Machines are outfitted with guards for a reason. These pieces are integral to ensure that the workplace is as safe as possible. Make sure that your workers are familiar with different types of guards and are aware of how to recognize issues or defects with them. Workers should never tamper with, remove or modify a guard.
Talk to a Workplace Safety Pro
We’re in the business of making your business safer. To learn more about workplace safety, talk to the manufacturing safety professionals at VTC Insurance Group. You can reach us at 248.828.3377 or visit vtcins.com.
This blog is for informational purposes only and is not intended as legal advice.